We have the most earthquake-resistant buildings in the world
The German construction industry is going through a severe crisis. High interest rates and expensive material costs burden the companies. However, Nora Baum sees signs of recovery: "Concrete plants are investing again", says the CFO of the Cottbus concrete company Sonocrete* in the "Climate Lab" of ntv. "They expect to create new construction again soon." Construction, which will be greener and cheaper than before. Because concrete is produced with Sonocrete's Ultrasound machines, significantly less cement is required. Not only is it dirty (five to eight percent of global CO2 emissions), but it is also expensive due to high temperatures. "We save money with our technology after approximately five years", says Nora Baum. What is still missing for the German construction boom? Fewer regulations: "In Germany, no buildings collapse due to an earthquake."
ntv.de: When is the construction crisis over?
Nora Baum: I unfortunately don't have a crystal ball, but our main customers are concrete plants. Their investment budgets were cut last year. There is a gradual pick-up, investments are being made again. This makes me optimistic that the industry could be on the upswing by the end of 2024 or early 2025.
Are these investments going into new construction?
Concrete plants usually invest in their plant technology. They only do this when they expect their sales basis to stabilize. They therefore expect to deliver concrete for new construction again soon.
Then the industry has passed through the trough.
Either that or we are in the process of doing so. We certainly hope so. In this assessment, there is certainly a portion of optimism.
And what exactly do your customers get when they invest in you?
Our technology is a high-performance ultrasound premixing plant. It's a long word (laughs). In it, water and cement are mixed. Those are the two reactive components when making concrete. Sand and stones are added for strength. This high-performance ultrasound has the astonishing property of being able to accelerate almost any chemical reaction.
High-performance ultrasound?
Ultrasound is like sound waves, but with a different frequency. By generating sound waves in a liquid, one creates alternating overpressure and underpressure - like a long rod that moves back and forth in the nanometer range. When this is done in a liquid where a chemical reaction is taking place, the reaction is accelerated. That's why ultrasound is a common technology in medical technology or in wastewater treatment. When ultrasound is added to the water-cement mixture, the concrete sets faster. This is not very practical for concrete plants, as they have a fixed schedule and timing for casting and removing concrete components. But we use the effect to use less cement in the mixture and save CO2 as a result.
So the concrete doesn't set any faster, but less material can be used and that's better for the environment and saves money?
Yes, that's correct. The concrete sets just as slowly as before, the optimization step is the cement amount. The high CO2 emissions of the construction industry are due to cement production. Cement production is responsible for five to eight percent of global CO2 emissions.
And how does this ultrasound process work in practice? Does it happen in the concrete mixer?
We wanted to do that at first, but it makes no sense in a concrete mixer because sand and stones are already part of the mixture there. They swallow a large portion of the ultrasound energy and also damage the very expensive ultrasound transducers. That's why our machine is standing by. It's a huge cube: six meters high and three by three meters wide. Inside is a barrel, into which the water and cement come. From the bottom, these ultrasound transducers protrude. After a certain time, the mixture is filled from the barrel into the concrete mixer.
Does this happen on site at construction sites or still at concrete plants?
Concrete has two well-known production methods. The first is fresh transport concrete in a concrete mixer, which must be transported quickly to the construction site and poured there before it sets. We currently only work in the precast concrete sector. The process is the same, but everything happens in the factory and at the end comes out a finished product: a wall, a pillar, a carrier.
Because it can be planned better?
There are several advantages: The industry is suffering from a severe labor shortage. In a factory, it is always warm and dry, which makes it easier to find workers. They can also be better planned and deployed there than on changing construction sites. The production processes can also be better automated in a factory. This results in higher concrete quality.
Your ultrasound concrete is also "greener" concrete. How much cement can be saved with that?
The reactive component in cement is cement clinker. With our method, we can reduce the required amount of clinker by approximately 30%. The additional energy consumption for ultrasound is negligible. If you do it in the factory, you can operate the machine with solar energy from the roof. That's a fully green solution.
And your concrete is also cheaper than conventional? That's often the problem with green solutions and it also happened with heat pumps: They are more sustainable than a gas heating, but in many cases also more expensive. That's why they were deliberately avoided.
Yes. With many green technologies, there is a surcharge, the so-called Green Premium. These technologies depend on the fact that CO2 is fairly priced. The CO2 pricing was long considered a paper tiger, where people thought: My goodness, what a regulation, that brings nothing. But suddenly, the CO2 price had jumped to over 60 Euros and the phones started to heat up because the concrete plants refused to pay this high CO2 price. But as I said, our advantage is that we can reduce the required amount of cement clinker. It is already quite expensive in its production because high temperatures are required. Therefore, our technology pays off after approximately five years. After that, you save money.
The core problem, the increasing construction demand, will not be solved by that, or? There are 43.1 million housing units in Germany. The stock has increased from 1950 to 2021 almost threefold because more and more people live in Germany and also more and more alone. Do you have an idea for that?
It wouldn't make sense from a concrete perspective to demolish a house after 30 or 50 years and build a new one because the concrete gets better. The chemical reaction that takes place between cement and water every day makes every house stronger.
And it will get better. Some old houses may not be pleasing to our taste, but that is ultimately just a matter of aesthetics. The concrete could continue to be poured loosely. That wouldn't be a problem. But in the end, it's likely that startups like us won't focus on how much one builds, because construction can be made as eco-friendly as possible through our and many other solutions.
What other solutions could this be?
That's an unsatisfying answer, but in principle, the entire value chain of construction needs to be involved. So far, the goal has always been to make construction as safe as possible.
That doesn't sound strange at all.
No, but in Germany, we have the world's safest stock of residential buildings when it comes to earthquakes. I've experienced very few earthquakes here. These requirements must be weighed, because there is no limit to safety. One can always build safer and safer and safer. Therefore, excessive building materials are sometimes used. This is not just for concrete, but also for wood.
Less regulation would be sensible? This is a demand often heard in the industry.
Yes. This regulation didn't grow out of malice or because people are stupid. It was pursued because of the goal "Safety." Therefore, in doubt, the higher exposure class was chosen. It specifies what a building component must withstand. The toughest exposure classes are for concrete components that are regularly flooded with water and then dry out: landings on the Baltic Sea or the side elements of a motorway, where salt spray regularly sprays. These are extreme requirements. Foundations in residential buildings also have a high exposure class because they carry the load. Walls, on the other hand, hang between these foundations. They hold almost nothing.
And could they be thinner?
Or made of concrete that contains less cement and is more eco-friendly. This component should be added to the regulations, because no buildings in Germany collapse due to an earthquake.
Clara Pfeffer and Christian Herrmann spoke with Nora Baum. The conversation was shortened and smoothed out for better understanding. The complete conversation can be heard in the podcast "Climate-Lab"*.
The investment in Sonocrete's Ultrasound machines by concrete plants indicates a potential recovery in the construction industry. This is due to their expectation of delivering concrete for new construction again soon. (Nora Baum)
However, while Sonocrete's technology can save money and reduce CO2 emissions by using less cement, it doesn't directly address the increasing demand for housing in Germany. (Nora Baum)
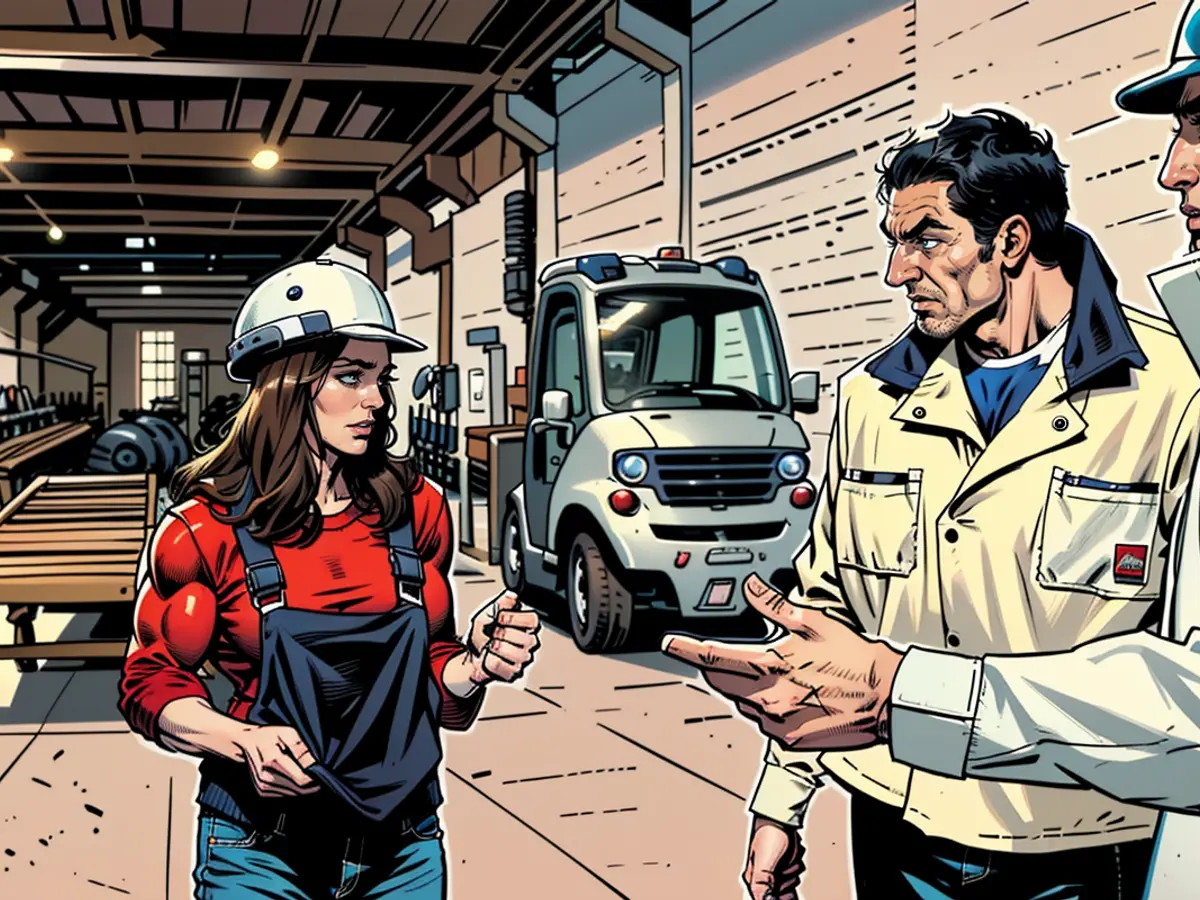