"There is no business case for saying goodbye to gas"
Dirostahl looks back on a tradition of over 400 years in the industry. In the 16th century, the heavy hammers of the Remscheid steel mills were moved by water power. Over time, coal and oil followed. Now, Dirostahl heats tonnage-sized workpieces with natural gas to 1200 degrees Celsius, so they can be formed and used as components in wind turbine generators. "We are aware of the idea of a fuel switch," says Roman Diederichs. However, the Dirostahl CEO is at a loss. For now, a clean alternative to natural gas, preferably green hydrogen, is required before it can be used in the real smelting furnace. This has only worked in the lab so far, says Diederichs in the "Climate Labor" of ntv. And expensive: "When you're in international competition, these additional costs cause significant problems." These problems could lead to wind turbine components coming from abroad - and continuing to work with gas.
ntv.de: What is Dirostahl's energy consumption?
Roman Diederichs: It depends heavily on utilization, but we are in the order of magnitude of 15 Gigawatt-hours (GWh) of electricity and between 150 and 200 Gigawatt-hours of natural gas. This corresponds to the consumption of 10,000 households in a year.
And now you need an alternative to natural gas.
Currently, forges are operated with natural gas. Various companies in this industry are considering what alternative heating media could be. Some together, some individually. When the material comes out of the furnace, it must be at a temperature of 1200 degrees to be formed. This doesn't work with every medium.
Can such high temperatures be reached with electricity?
It depends on the dimensions of the workpieces. Automotive suppliers typically work with drop forging, to produce parts with low weight in large series. The weight ranges from grams to kilos. These parts can be heated inductively, i.e., with electricity. This only works up to a cross-section of around 240 millimeters. That's about the size of a hand span, which can be grasped with the hand. Larger parts cannot be heated efficiently and in a reasonable time with a reasonable energy input inductively.
And the parts you produce for the wind turbines are likely to be larger?
Yes, we work with a forge and process medium-sized parts, which weigh between 500 kilograms and 8 tons. The total weight range is from 50 to 35,000 kilograms. Often, they are seamless rings: First, the pre-product must be formed to create a forging ring. This is then further forged. Once this process is mastered, one can work with heat or with the residual heat. If it doesn't go well, the piece must be heated twice.
And that only works with gas at the moment?
Yes, in these dimensions. Of course, one can also consider other technologies such as resistance heating, hydrogen, or hot air. Startups, as well as established companies, have various ideas. However, they all have their advantages and disadvantages.
The alternative that is mentioned most frequently in response to this question is green hydrogen. Federal Chancellor Olaf Scholz and Federal Minister of Economics Robert Habeck have traveled around half the world to sign supply contracts. That doesn't work?
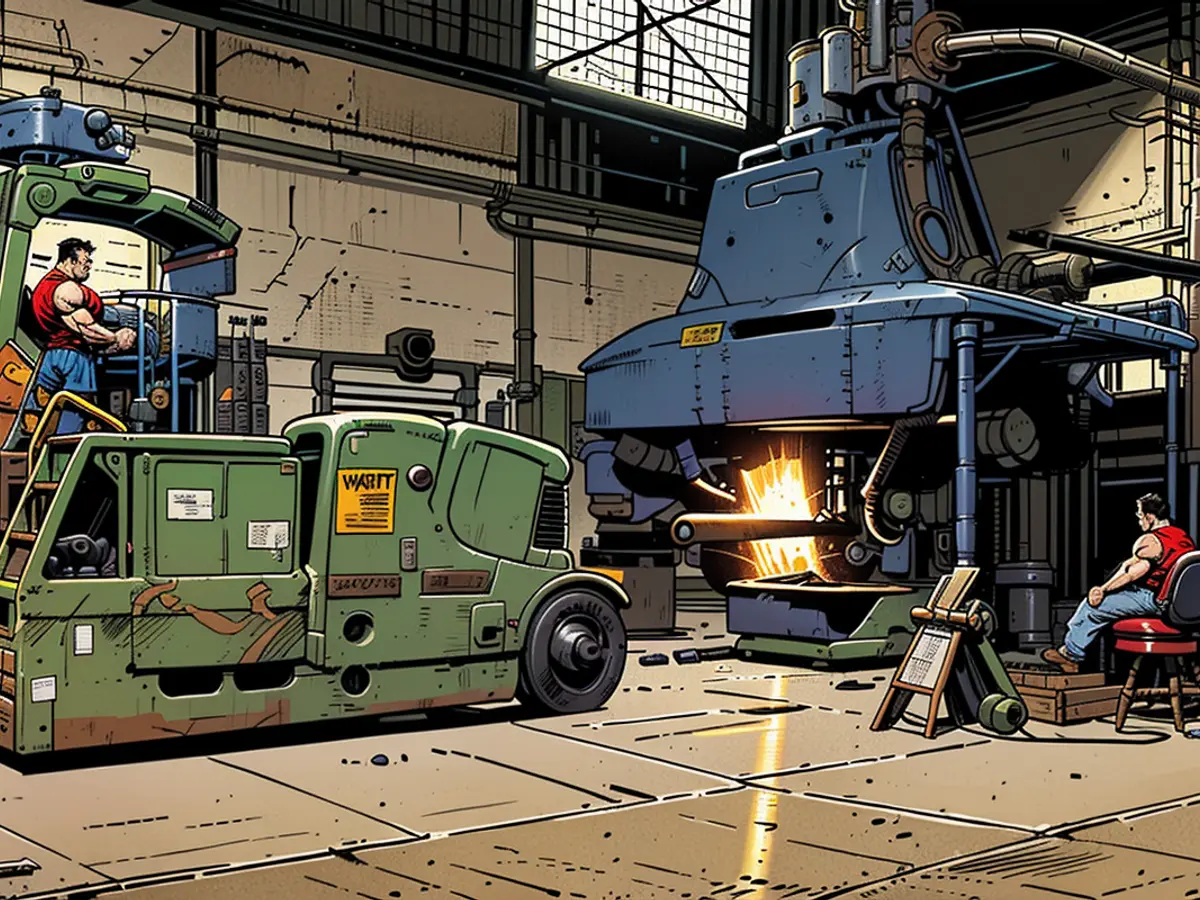
One must look where one comes from. If one produces green hydrogen locally with green electricity, one has a significant cost disadvantage: Compared to natural gas, green electricity is already relatively expensive. One then has to double this price to get to the hydrogen price. This is what is being circulated. It will also be shown whether an electrolyzer pays off if it does not run 24 hours a day. Similarly, which import quantities of green hydrogen eventually come to what conditions on the world market.
But technically would it work? Can green hydrogen be used instead of gas in the same machines? They shake their heads ...
There are many studies on hydrogen use in burners. There they try to generate process heat with natural gas-hydrogen mixtures or pure hydrogen use. In the lab scale, it works - with some technical restrictions; on a large scale, it is difficult so far. There are various attempts by different institutions, but also companies. One must look at the risks and side effects of hydrogen use. Many components are hydrogen-compatible or should be, but the approvals only allow 20 volume percent hydrogen in natural gas. There are also technical parameters such as adiabatic flame temperature ...
... adiabatic flame temperature?
Yes (laughs). Natural gas burns at approximately 1900 degrees Celsius, hydrogen at 2100 to 2200 degrees. That's no big problem in the furnace. However, nitrogen reacts in the furnace atmosphere to nitrogen oxides. At a higher adiabatic flame temperature, nitrogen formation increases significantly. One must therefore pay attention to not producing nitrogen as a byproduct in the exhaust gas in significantly higher concentrations.
Can nitrogen oxides be filtered out?
Once they have been formed, it will be difficult. Therefore, one must keep the thermal nitrogen oxide formation in check, which goes over the burner control and temperature control. There are therefore some parameters to consider.
And is that expensive?
It depends. If one works with pure oxygen, one has a more expensive feedstock than if one works with combustion air. The latter can also be heated more effectively. That's a question of energy efficiency, and yes, in the end, more money has to be invested in burner technology.
Could one replace the gas with hydrogen in any case?
If there is sufficient hydrogen and reliable supplies, I am sure we will master the technology, even if some open questions such as nitrogen oxide formation need to be considered. However, significant economic problems remain.
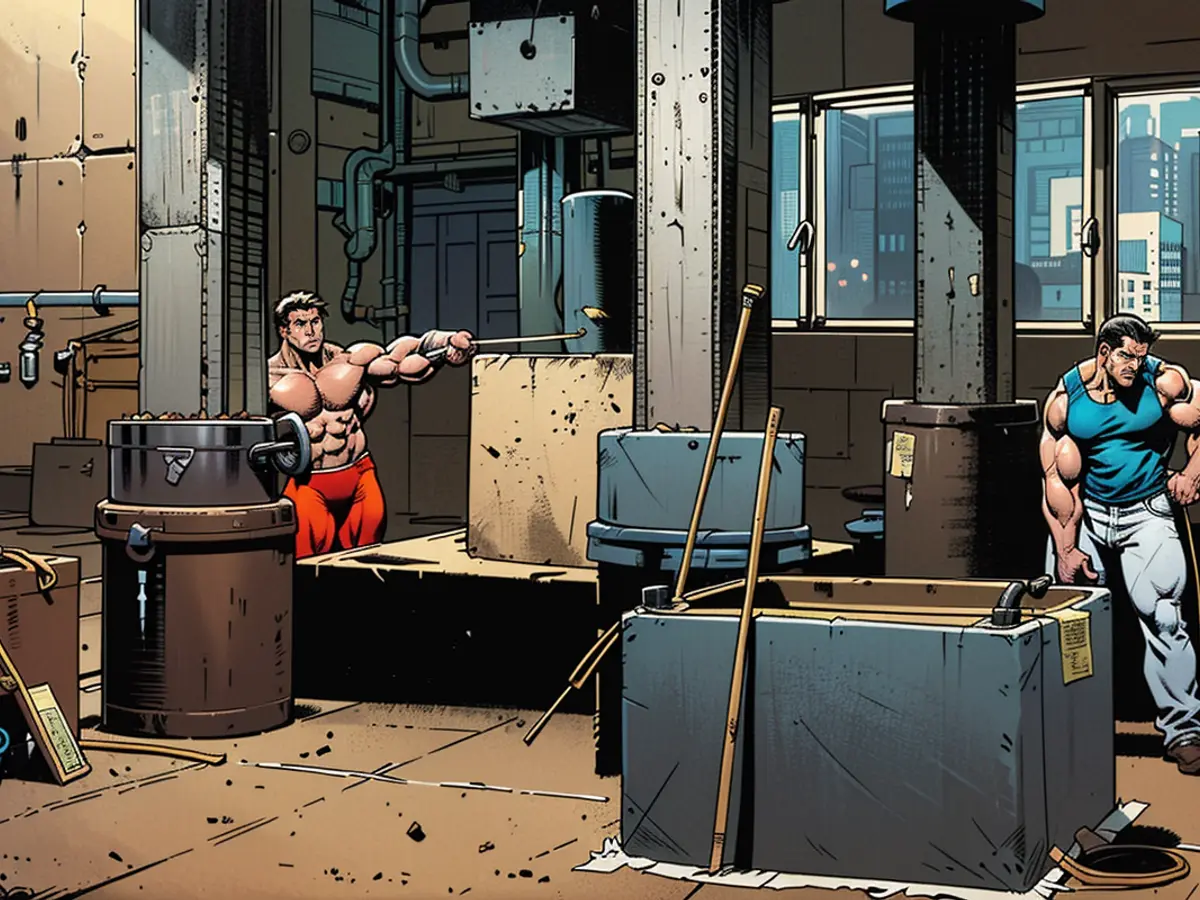
What is the current status with you? Are you still betting on green hydrogen? Are you experimenting? Are you trying to get hydrogen for Dirostahl?
Of course, we keep an eye on the topic. We have also filed an application to get a handle on these parameters, so that we are ready when there is enough hydrogen available. Economically, one must consider that hydrogen currently costs approximately three to five times as much as natural gas. When one is in international competition with wind power products, these additional costs cause massive problems up to the point of unprofitability in production.
Are there plans to bring hydrogen from Chile, Morocco, or Oman to Remscheid? Do you need a pipeline?
There are various models. Whether there will actually be hydrogen production in Germany, lies beyond my horizons. Currently, we assume that a pipeline is needed for hydrogen supply. This will be discussed in the Bergisch Land at the beginning of the 2030s.
Do we have to build that?
There are also different models here. It is being tested if an existing gas pipeline can be converted and expanded. It could also be a new build, but that has to be answered by the respective utilities.
The Federal Ministry of Economics is working intensively on covering the increased costs of the green steel industry. That will be very much subsidized. Is that enough?
There are some programs that support such a transformation, but one has to look if a medium-sized company can afford it. Thyssenkrupp has other possibilities. One cannot subsidize everything that needs to be converted for 15 to 20 years. For that reason, the budgetary resources will not suffice.
We have experienced some transformations in the past centuries. In the Bergisch Land, there are many valleys and sufficient rain. Previously, streams were dammed, water wheels were built, and small forges and grinding mills were operated with water power. Later, hammers were operated with steam from coal. In the 50s, we switched to nuclear power, and in the 80s, to natural gas. We are familiar with the idea of energy transition. However, what is important for the transition is a positive business case. There isn't one at the moment, rather ambitious goals. So it will be high risk.
If the plans are implemented as they currently look, are you no longer competitive in the end?
This risk exists in the energy-intensive industry, if one actually sets the wrong horse. Definitely. We have already lost the photovoltaic industry in Germany, and next, we must certainly be careful in the wind energy industry. One cannot afford to arbitrarily increase energy costs there.
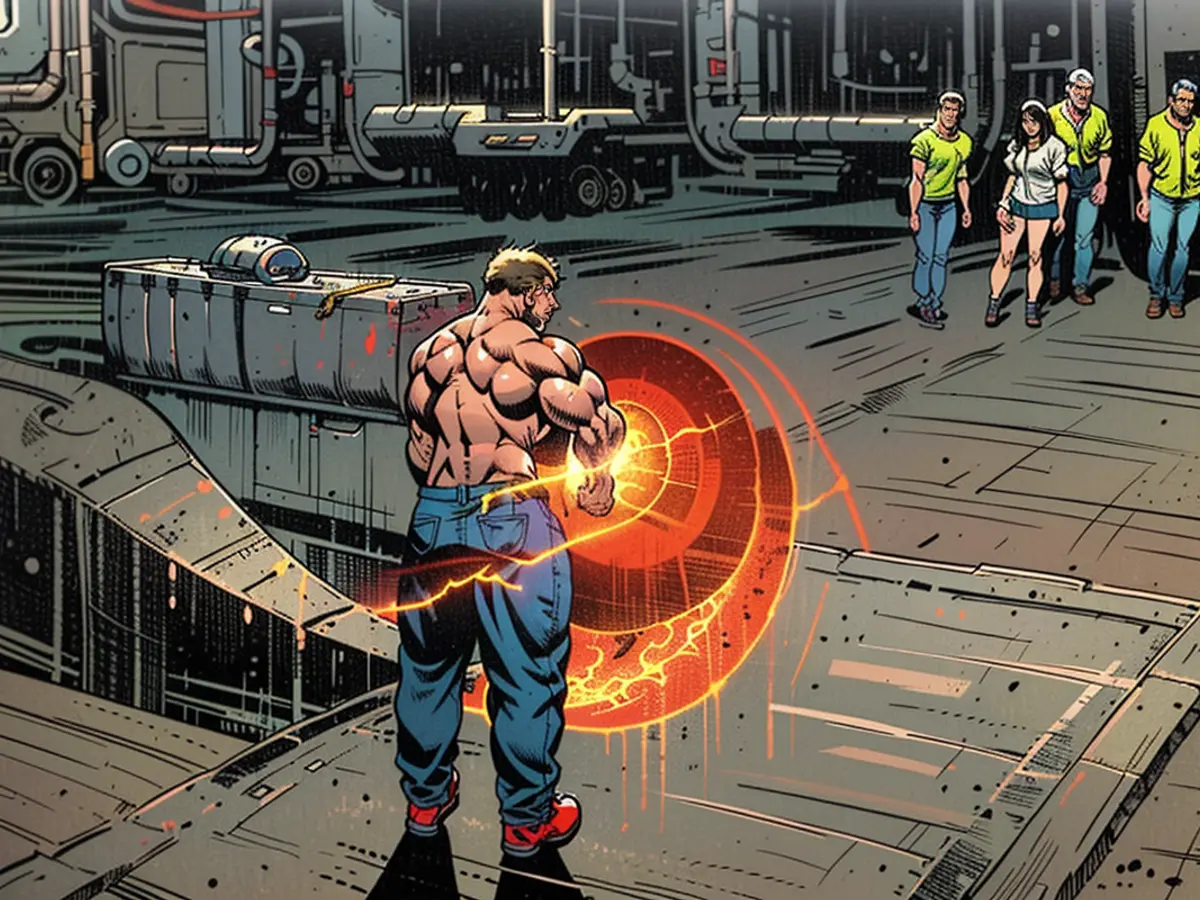
Clara Pfeffer and Christian Herrmann spoke with Roman Diederichs. The conversation was shortened and smoothed out for better understanding. The complete conversation can be heard in the podcast "Klima-Labor".
- Roman Diederichs, the CEO of Dirostahl, expresses the need for a clean alternative to natural gas, preferably green hydrogen, in order to reduce their reliance on fossil fuels for heating tonnage-sized workpieces used in wind turbine components.
- ThyssenKrupp, a company in the steel industry based in North Rhine-Westphalia, is also considering alternative heating media to natural gas for forges, as green hydrogen is mentioned as a frequent alternative due to its potential to reduce carbon emissions.
- In the search for a clean alternative to natural gas, Remscheid's Dirostahl has filed an application to explore the use of green hydrogen, recognizing that the current cost of hydrogen is significantly higher than natural gas but acknowledging the potential long-term benefits.