In our buildings, boilers will never be turned on again
With the current pace, nearly less than 100 years are left until the German building stock is energy-refurbished. Emanuel Heisenberg promises a solution that makes it faster: His company Ecoworks is bringing in modular housing manufacturers for the serial refurbishment of apartment buildings in the east and the west. "On their production lines, exterior walls for the serial refurbishment are running now", Heisenberg says in the "Climate-Lab" of ntv. "And with an incredibly high quality that cannot be achieved with craft refurbishment."
The result sounds too good to be true: According to Heisenberg, energy consumption decreases by 90 percent with the new building envelope. If these are additionally equipped with solar panels and heat pumps, they generate significantly more energy than they consume. "That's a whole new feeling", swears the Ecoworks CEO.
Criticism from the conventional refurbishment industry about the serial approach is ignored by Heisenberg: "Even with wind and solar, it was said at the beginning that it was a pipe dream", Heisenberg says. "Now they're nitpicking about costs, but we'll bring those down too, it's just a matter of time."
ntv.de: To what extent can serial refurbishment help in sanitizing the German housing stock?
Emanuel Heisenberg: We focus on multi-family houses first, because we need large projects to justify the planning and production costs. There are 43 million housing units in Germany. Approximately half of them are in multi-family houses. From this half, we can refurbish 8 million serially.
That's about 36 percent of all housing units in multi-family houses. How exactly does it work?
We are focusing on buildings that are not architecturally very beautiful, as we want to make them not only more efficient but also more attractive.
So you mean panel buildings?
Absolutely, we are currently scanning a panel building in Berlin-Marzahn. We scan the buildings from the inside and outside with a laser. Then we receive a point cloud, or a digital twin. With our planning software, which we have further developed with artificial intelligence (AI), we can design a second shell almost entirely automatically, which we build around the existing building.
The panel buildings in East Berlin are relatively large. Most of them have six floors, but in Marzahn, there are often eight or even twelve. How long does the scanning take, when a digital twin must be created for each apartment?
It can take several days because everything needs to be millimeter-precise. The actual construction time is then 12 to 15 weeks. The assembly of the second shell takes 2 to 3 weeks.
And which part of this process is serial? Under the term "series production," one understands a cost-effective series production. Measuring each wall and apartment accurately to the millimeter seems to be the opposite.
In the automotive industry, they also build in series, on average, only 1.4 cars are identical, so not really. There are always small deviations. The same applies to buildings: The external design or individual engineering properties of the shell can deviate; perhaps there is a cellar staircase in one building and not in another. But all buildings share the same platform: The elements have a load-bearing structure, as do the windows and other elements.
One of our largest innovations is that we have managed to motivate an entirely new industry for the refurbishment and now use their factories for the production of our elements: Prefabricated housing manufacturers. I was at Bien-Zenker last week. They belong to the Oikos Group, which in turn belongs to Goldman Sachs. This is a large prefabricated housing conglomerate for single- and two-family homes. This sector currently has a massive economic problem. Therefore, the management of Bien-Zenker said: Let's produce modules for serial refurbishment. Now, these huge lines no longer produce prefabricated house walls from the band, but walls for serial refurbishment; and with an incredibly high quality that cannot be achieved with craft refurbishment and at significantly lower costs.
But isn't it still not being refurbished? The quote is at 0.7 percent. Which parts are they producing?
We are working on a pipeline of orders in the three-digit million range and passing these orders on to the prefabricated housing manufacturers.
And unlike the rest of the construction industry, do you have the necessary working capital and the necessary skilled labor for these projects?
The problems in the construction sector are enormous because labor and materials are becoming increasingly expensive. Historically, neither labor nor the costs for windows or insulation have ever been cheaper. Therefore, it is important that we make refurbishment affordable. If we move 80 percent of the work into the factory, craftsmen no longer have to perform individual work steps, robots do. Through the strong standardization of components, we can also obtain the components at a fraction of the cost compared to a craft business. This creates an entrepreneurial, but also a societal added value.
What effect do these refurbishments have? How much does energy consumption decrease?
After refurbishment, 90 percent of primary energy is saved. This energy is needed to heat a building and generate electricity for it. If a photovoltaic system is installed on the roof and a heat pump in the basement, this object generates up to 30 percent more energy than the tenants need for heating, hot water, and electricity.
Do the residents only save energy by insulation?
Exactly. They also save a lot of energy with normal energy-saving refurbishments, but in Germany, over 50 percent of oil-based insulation materials are still used. These are called EPS in technical jargon, in the vernacular Styrofoam. When it is glued, many new, so-called grey emissions are created. These elements often end up in special waste. Our elements are mainly made of wood, the insulation is made of cellulose. In terms of emissions, our facades are 37 times more efficient than a craft refurbishment with oil-based insulation elements. Our shell also has a circular design. It lasts 50 to 70 years, then the individual layers can be separated and recycled.
Do you already know that?
There are advanced window manufacturers like Schuco, who even give a take-back guarantee. In countries like Denmark, these grey emissions are already regulated. There, it is not only looked at how many process emissions are saved after refurbishment in energy production, but also how the shell was manufactured.
The panels you start with are, however, those that need to be refurbished the least. In fact, you are handling the easiest task. The challenging cases would be old buildings and buildings from the founder era.
We focus on the system buildings from the 50s to 70s. These are often referred to as "WBS-70 buildings". Engineers back then had already built in a light insulation, making eastern German construction more energy efficient with an efficiency class C or D, while western German construction was more like G or H. We achieve the highest energy savings in 80% of our orders for these buildings.
It sounds too good to be true. Why isn't this done everywhere?
It's nice that it sounds simple, but operationally, it's incredibly difficult to install modules in the ceilings and to get budget, time, and quality on our 19 construction sites with over 1000 housing units so that it can be scaled. We have managed to reduce costs by 28% in the past two years, but they are still the biggest challenge. If we want to further reduce the subsidy, we have to scale it up even more. The federal government also needs to open up and allow functional buildings and administrative buildings to be repaired serially, so that we can make it work for people without it becoming a burden.
Can we afford to wait on politics? Hear from companies that conventionally repair: "Serial repairing works at best in five to ten years. We don't have that much time. Why don't we just do what works? We have 50 years of experience with insulation. The craftsmen are waiting. Let's finally get started."
If you've been in these industries for a long time, you'll see the same patterns: Wind and solar were also initially dismissed as a pipe dream. Then it worked, and it was said to be too expensive. Then it became cheaper, and it was said that birds suffer and wind turbines are ugly. The same was said about us that serial repairing is nonsense. Then we made the first repair, which generated 25 to 30% more energy than was consumed. Now they're talking about costs. We'll bring those down too, it's just a matter of time.
But do we have that time? In Germany, there are 15 to 16 million single-family and two-family houses, where almost nothing has happened. What do you offer them?
We won't repair those buildings, our solution is aimed at multi-family houses. We offer the housing industry the opportunity to provide affordable, climate-neutral living space with fewer skilled workers, AI, and smart tools. That's all.
And who pays for the costs of these measures for the people in the apartments?
We have cooperatives that do not increase the rent, but only the cold rent in proportion to the decrease in ancillary costs. We also have commercial landlords who significantly increase the rent. That's outside our influence. But through the repair, we also create additional living space, as balconies or extensions are created. The living standard and comfort increase significantly. Children do their homework better in these apartments than in an old building, where it might even be moldy. That's a different feeling of life.
And for this feeling of life, how long do people have to be out of their apartments?
In this second shell, everything is pre-fabricated. The windows are in place, insulation, even wiring for the heating elements. On the day of installation, we hang plastic film on the surfaces around the windows in the apartments, then we cut out the old windows, insert the pre-fabricated wiring, roll them up and connect the electronics, and then we plaster everything over. In about 90% of the apartments, we can even reuse the old wiring and heating bodies, but to be honest: In almost all objects that we have sanitized, the heating bodies will never be turned on again.
Clara Pfeffer and Christian Herrmann spoke with Emanuel Heisenberg. The conversation was shortened and smoothed out for better understanding. You can listen to the entire conversation in the podcast "Climate-Lab"*.
- Emanuel Heisenberg aims to refurbish a significant portion of the 43 million housing units in Germany, focusing on multi-family houses, as they provide large projects to justify the planning and production costs.
- To achieve this, Ecoworks is collaborating with prefabricated housing manufacturers to produce the required elements for serial refurbishment, which are more energy-efficient and cost-effective than traditional craft refurbishments.
- With the new building envelope and the addition of solar panels and heat pumps, the energy consumption of these apartments can decrease by up to 90%, and they can generate more energy than they consume.
- According to Heisenberg, modernizing the building stock with serial refurbishment could help meet Germany's Heating Law requirements, which aim to make nearly all buildings energy-efficient by nearly 100 years from now.
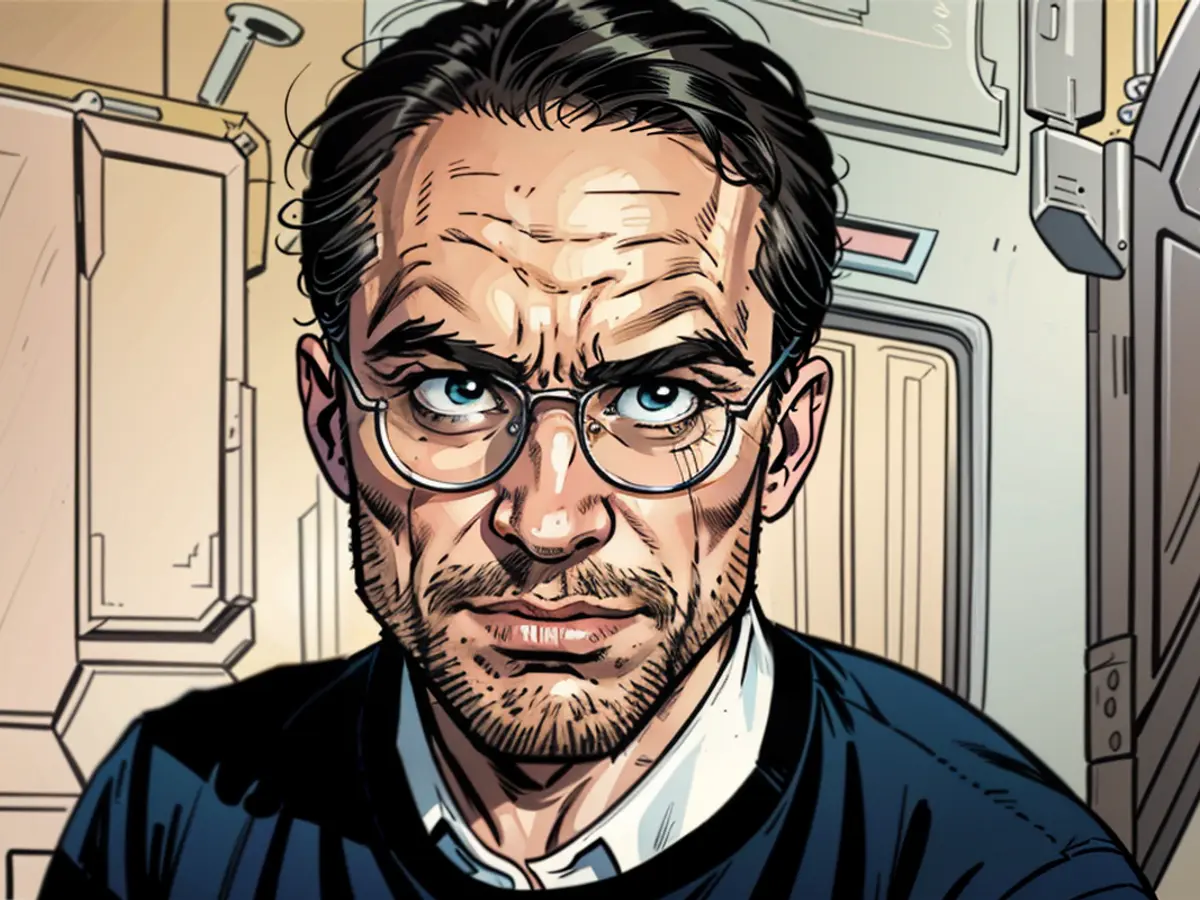